Tube Furnace for Battery R&D
SH Scientific tube furnaces equip you to work on the frontiers of battery technology.
With comprehensive programmability and complete gas flow control, our turn-key solutions are optimal for sintering, annealing, and even CVD graphene production.
What’s a Tube Furnace?
A tube furnace contains a central cylinder (the “tube”) surrounded by electrical heating elements, which are generally connected to a programmable, digital controller.
The tube and heating elements are all made of temperature-specific materials that provide the right balance of cost and longevity for the intended operating conditions.
The Role of Tube Furnaces in Battery Development
The batteries of the future are solid-state.
In fact, solid Li+ ceramic electrolytes are poised to solve many of today’s biggest challenges with energy storage, from fire hazard to longevity to energy density.
But building the future requires novel techniques today. For instance, producing solid-state ceramics under 700°C may yield better control over lithium-oxide thin film structures. Eventually, liquid-based densification, vacuum processes, and grafting may even replace the classic (and much hotter) methods of sintering and calcination.
These lower-temperature techniques promise better control over conductivity, which ultimately means safer and more efficient batteries.
Of course, reliable ceramic electrolytes depend on the purity and structural integrity of their materials, so tube furnaces are essential for R&D.
And at SH Scientific, we’re proud to serve innovators in the design and manufacturing of low-cost solid-state batteries.
So what role, exactly, do our tube furnaces play?
Thermal Treatment Overview
In the battery world, tube furnaces are widely used for synthesis of materials, debinding, calcination, and drying.
The process comprises three main steps:
- Pyrolysis
- Carbonization
- Graphitization
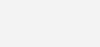
Pyrolysis generally takes place between 200°C-400°C, but potentially up to 900°C. This stage forms a lot of off-gases, so the furnace must be ventilated to keep the chamber’s atmosphere pure.
– For pyrolysis, we recommended the SH-FU-STG/LTG series of tube furnaces (max temperature: 1200°C).
– For carbonization, we recommend the SH-FU-TH (max temperature: 1500°C) or SH-FU-TS series (max temperature: 1800°C).
– For graphitization, please send us an inquiry.
Sintering
One common use of tube furnaces is to prepare ceramic for use in electrodes and even solid electrolytes. The ceramic needs to reach an extremely dense state, which is generally achieved through sintering.
Standard sintering techniques may require temperatures close to 2000°C, with high uniformity throughout the heating chamber. A tube furnace is the easiest way to manage these extreme temperatures, especially for the relatively small samples that most battery components use.
Annealing
Many traditional and solid state batteries contain specialized alloy components. These are subjected to thermal annealing, which removes irregularities that would jeopardize performance and/or safety.
Oxidation and temperature fluctuation can undermine the annealing process, so many laboratories employ a programmable tube-furnace with inert-gas management.
Monolayer Graphene via CVD
Graphene is a relatively new material at the cutting edge of battery technology. It’s often produced through chemical vapor deposition, or CVD. This process involves heating a substrate before introducing a volatile metal gas, which decomposes and adheres to the substrate. A second gas—usually hydrogen—is introduced to react with the adhered molecules, forming a waste gas and leaving the metal atoms behind. Slowly, those remaining atoms accumulate into a usable graphene monolayer.
Tube furnaces are often the environment of choice for CVD. The nature of the reaction (and the toxicity of its by-products) means gas flow and vacuum control are critical.
Why Use an SH Tube Furnace?
Battery R&D revolves around several delicate thermal treatments. Every SH furnace provides fully programmable temperature control, with rapid heating/cooling and high uniformity you can trust.
We equip battery labs with:
- Programmable digital controller for one-, two-, or three-zone use (up to 1800°C at +/-1°C uniformity)
- Up to four ball type gas flow meters, upgradeable to a digital mass flow controller and back pressure regulator
- Low-noise vacuum pump for peaceful, focused working conditions
- Optional recirculating chiller
- Several tube and hot-zone sizes to suit your facility
We’re proud to offer Korea-built, USA-supported tube furnaces to today’s leaders in energy storage research.
To discuss detailed specifications or request a custom quote, please contact us today.