Masterbatch testing & analysis
Super engineering plastics offer extraordinary performance, often on par with metals and more exotic materials.
Compared to commodity plastics, these lightweight and customizable alternatives require a more complex and expensive manufacturing process. With significant production costs on the line—not to mention end-user safety—testing and quality control are of the utmost importance.
Tests often include:
- Masterbatch and carrier residue analysis
- Dry ashing to measure content and purity
- Softening and ignition point verification
- Temperature-dependent mechanical analysis
- Heat aging and weathering to ascertain durability
- Off-gas analysis
A muffle furnace is ideal for processes like ashing, which requires very high yet extremely precise and stable heat (potentially approaching 800°–900° C). This article will take a brief look at common testing protocols, then discuss the role of muffle furnaces in masterbatch/additive testing.
Masterbatch testing & analysis
Raw polymer seldom looks or performs the way a customer desires. From simple color changes to static control to life-saving flame retardance, a finished super engineering plastic generally includes multiple additives.
It’s not always desirable to work with raw additives. For instance, batch sizing and precision are common challenges. Conversely, pre-compounded polymers are a far simpler alternative, but potentially slow, costly, and inflexible.
Masterbatches provide a middle ground. Neither wholly custom nor wholly pre-mixed, they enable rapid customization and testing while avoiding constraints on batch size or shelf life.
However, masterbatches and final polymers both require careful analysis. Carrier materials may have undesired effects on the finished plastic, so it’s important to quantify their contents and detect byproducts that may impair the finished product.
ISO Testing Standards for Plastics
ISO 3451 is a common standard for plastic ashing. It prescribes up to 200 minutes in a muffle furnace at either (600 ± 25)°, (750 ± 50)°, (850 ± 50)°, or (950 ± 50)° C.
Depending on the polymer or masterbatch at hand, technicians may use one of four methods under ISO 3451:
- Method A: burning (by flame or muffle furnace) followed by calcining a muffle furnace
- Method B: burning, sulfuric acid treatment, and finally heating
- Method C: sulfuric acid treatment, burning, and finally heating
- Method D: use of an automated instrument
In any case, the main goal is to measure the amount of an additive or filler. Secondarily, the chemical composition of the ash can give further insight into the composition and behavior of, e.g., the masterbatch’s carrier.
While the allowable temperature variation is fairly high, most manufacturers prefer furnaces that maintain much narrower ranges. Pragmatically, rapid heating is also important for facilities that run frequent masterbatch tests.
Muffle Furnace Use In Masterbatch/Additive Analysis
Ash analysis from plastic combustion is typically conducted at temperatures under 900° C. Muffle furnaces can comfortably sustain this temperature range, all in a cost-effective form that’s also versatile enough for a wide range of other thermal treatments.
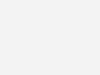
Our current models have maximum temperatures from 1050° C (generally recommended for additive/masterbatch analysis) to 1900° C, with equally high stability throughout the range. Preheating time is approximately 40 minutes to a typical ashing temperature of 800° C.
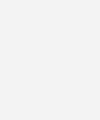
Currently, capacities range from 3 L to 36L, so there’s a cost-effective option for plastics manufacturers of all sizes.
We generally recommend smaller models for ashing and similar procedures. These fit comfortably inside a fume hood, so technicians can manage noxious fumes with standard, existing equipment.
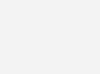
For assays that require environmental control, we offer ball type gas flow meters and (for most models) a programmable digital controller. And when perfect inert-gas saturation is required, our proprietary vacuum muffle furnace design rivals the performance of tube furnaces—with far higher capacity for the dollar.
Why SH Scientific?
Like every SH device, our muffle furnaces are built in Korea and fulfilled and supported from the West Coast.
Unlike most larger manufacturers, our low overhead lets us offer high performance at compelling prices. Yet unlike smaller equipment makers, we have the in-house design and manufacturing capabilities to offer essentially unlimited customization.
For technical guidance, or to discuss your polymer/additive workflow requirements with a specialist, please contact us today.